Injection Moulding
Through digital moulding, additive manufacturing can be seamlessly integrated into your existing manufacturing process as a replacement process for some small batch injection moulded parts. Through digital moulding, CAD designs are directly printed without the need for any moulding or tooling. Conformal cooling, an additive manufacturing technique, can also help with the tooling process. In additive manufacturing, more efficient cooling channels are designed into a mould that can then be printed. A higher cooling efficiency results in shorter cycle times, less waste, and fewer part deformities.
Conformal Cooling
Drilling can only produce straight waterways, limiting the shape of the waterway and its distance from the mould surface. Constructing complex lattice and waterways using 3D printing allows conformal cooling. Conformal Cooling allows the tool designer to precisely place cooling channels for maximum cooling efficiency. 3D printed moulds with conformal cooling channels dissipate heat faster than traditional moulds, reducing cycle time and increasing efficiency. Due to the high temperatures used in traditional manufacturing, parts are easily bent and deformed. Producing zero-defect products and reducing scrap with uniform heat dissipation is possible with additive manufacturing moulds. Tools like ejector pins and hot runner systems can be cooled in a way that minimises tooling disruption. Only 3D printing allows for this level of design freedom and performance.
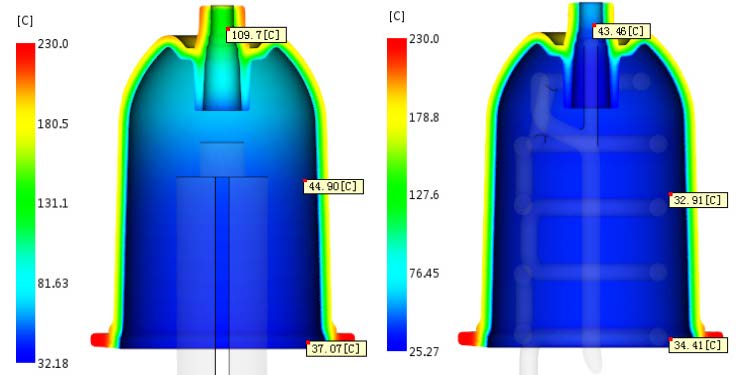
Digital Moulding
The digital moulding process is comprised of discrete modules for every step required in direct 3D production. Despite being around for 150 years injection moulding has always required tooling. Although it has been simplified and sped up by advances in CNC and 3D printing, the tooling of increasingly complex injection moulds is still measured in weeks and sometimes months. This all changes with digital moulding. This digital approach enables designs to go straight from CAD to manufacturing without tooling, facilitates on-the-fly iterations of part designs, accelerates production transitions to new designs without retooling, and rapidly manufactures parts that are too complex for traditional injection moulding.
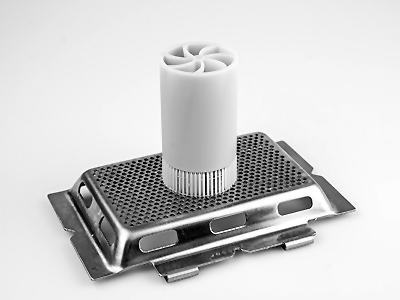